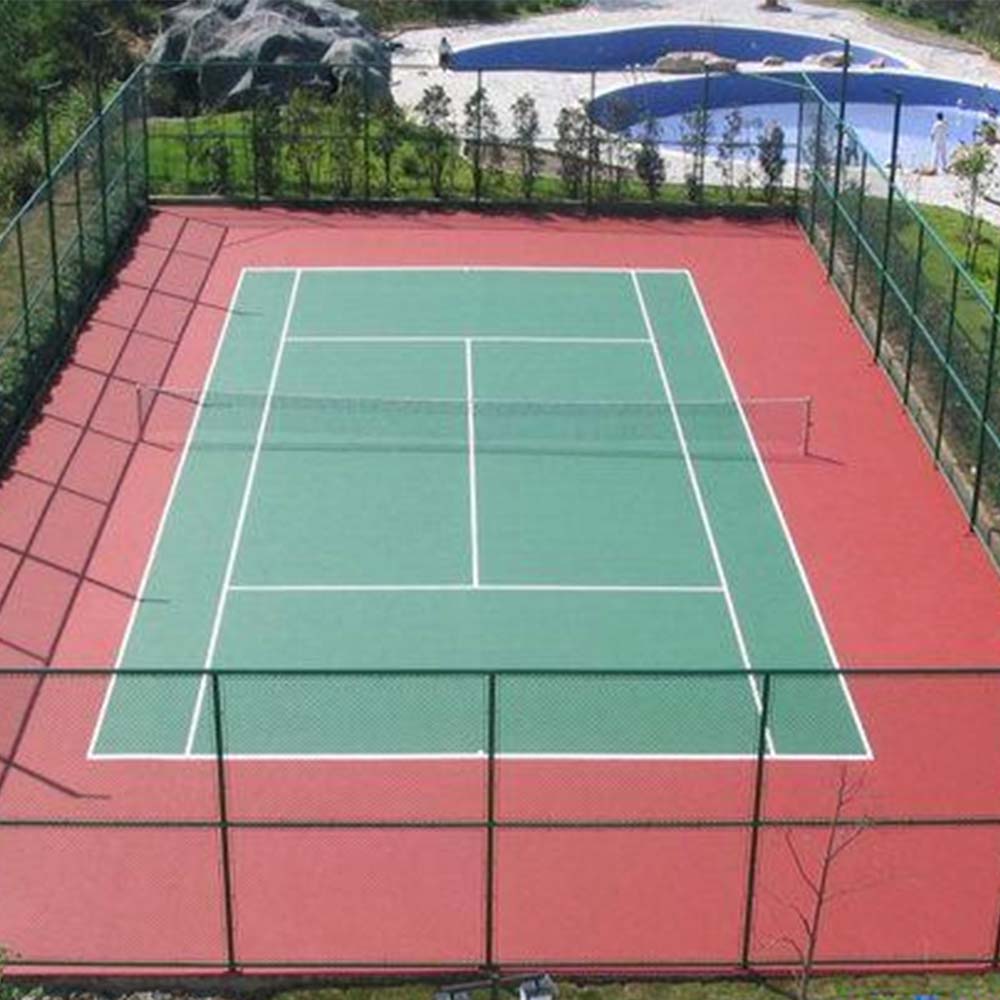
What is SBR Rubber Granules?
Table of Contents
Here’s a simple breakdown of the chemical composition:
Styrene: Provides hardness and strength to the rubber. Typically comprises around 25% of the SBR compound.
Butadiene: Provides flexibility and resilience to the rubber. Makes up the remaining 75% of the SBR compound.
The ratio of styrene to butadiene can be adjusted during the manufacturing process to create SBR with different properties. For example, a higher styrene content will result in a harder, more abrasion-resistant rubber, while a higher butadiene content will create a more flexible and resilient rubber.
How are SBR Rubber Granules Made?
SBR rubber granules are most commonly produced through the recycling of end-of-life tires (ELTs). This process, known as tire recycling or crumb rubber production, involves several key steps:
Tire Collection and Sorting: Waste tires are collected from various sources, such as tire retailers, auto repair shops, and landfills. They are then sorted to remove any non-tire materials and to separate tires of different sizes and types.
Tire Shredding: The tires are fed into large shredders that reduce them into smaller pieces, typically 2-inch chips. This initial shredding helps to remove steel belts and other large components.
Steel and Fiber Removal: Powerful magnets are used to remove the steel belts and wires from the shredded rubber. Aspiration systems and screens are used to separate the fabric and fiber reinforcement from the rubber.
Granulation: The shredded, steel-free, and fiber-free rubber is then fed into granulators. These machines use rotating knives or hammers to further reduce the rubber into smaller granules. The granulators can be adjusted to produce granules of different sizes, typically ranging from 0.5mm to 6mm.
Screening and Classification: The granulated rubber is passed through a series of screens to separate the granules by size. This ensures that the final product meets the specific size requirements for different applications.
Cleaning (Optional): Depending on the intended use, the SBR granules may undergo additional cleaning processes to remove any remaining contaminants, such as dust or small metal particles.
Ambient or Cryogenic Grinding.
Ambient Grinding: Ambient grinding occurs at or near room temperature. It’s the more common method due to its lower energy requirements and cost-effectiveness. The rubber is shredded and granulated using mechanical processes. While efficient for producing larger granules, it can result in irregularly shaped particles and may generate more heat.
Cryogenic Grinding: Cryogenic grinding involves cooling the rubber to very low temperatures (typically using liquid nitrogen) before grinding. This makes the rubber brittle and easier to shatter into smaller, more uniformly shaped particles. Cryogenic grinding produces finer, more consistent granules, and it’s often used when a higher quality or specific particle size distribution is required. However, it’s more energy-intensive and expensive than ambient grinding.
Applications of SBR Rubber Granules
Sports and Recreational Surfaces
Synthetic Turf Infill: SBR granules are the most common infill material for synthetic turf sports fields, providing cushioning, shock absorption, and stability.
Playground Surfacing: SBR granules are used in poured-in-place playground surfaces and rubber mulch to create safe and resilient play areas for children.
Running Tracks: SBR granules are often used in the base layer of running tracks, providing cushioning and support for athletes.
Walkways and Paths: SBR granules can be used to create comfortable and slip-resistant walkways and paths.
Equestrian Surfaces: SBR granules are used in riding arenas and other equestrian surfaces to provide cushioning and reduce dust.
Molded Rubber Products
Rubber Mats and Flooring: SBR granules are used to manufacture rubber mats and flooring for various applications, including gyms, industrial facilities, and animal care.
Automotive Parts: SBR rubber is used in various automotive parts, such as seals, gaskets, and hoses.
Industrial Components: SBR granules are used to produce a variety of industrial components, such as conveyor belts, rollers, and vibration dampers.
Asphalt Modification
Rubberized Asphalt: SBR granules can be added to asphalt to improve its performance and durability. Rubberized asphalt is more resistant to cracking, rutting, and thermal stress, resulting in longer-lasting roads and reduced maintenance costs.
Disadvantages of SBR Rubber Granules
Gets Dangerously Hot in Sunlight SBR granules trap heat, reaching up to 175°F (80°C) in direct sunlight. This causes burns on playgrounds and makes sports fields unusable during peak hours.
Contains Harmful Chemicals Recycled tire rubber in SBR may release heavy metals (like lead) and volatile organic compounds (VOCs). These toxins can harm plants, soil, and human health.
Short Lifespan SBR surfaces degrade quickly, lasting only 2–5 years. Repeated repairs and replacements increase long-term costs.
Bad Odors SBR emits a strong rubber smell, especially in heat. This drives users away from parks, gyms, or pool areas.
Fades and Stains SBR turns gray over time and leaves black marks on clothes. It also washes away in heavy rain, creating uneven surfaces.
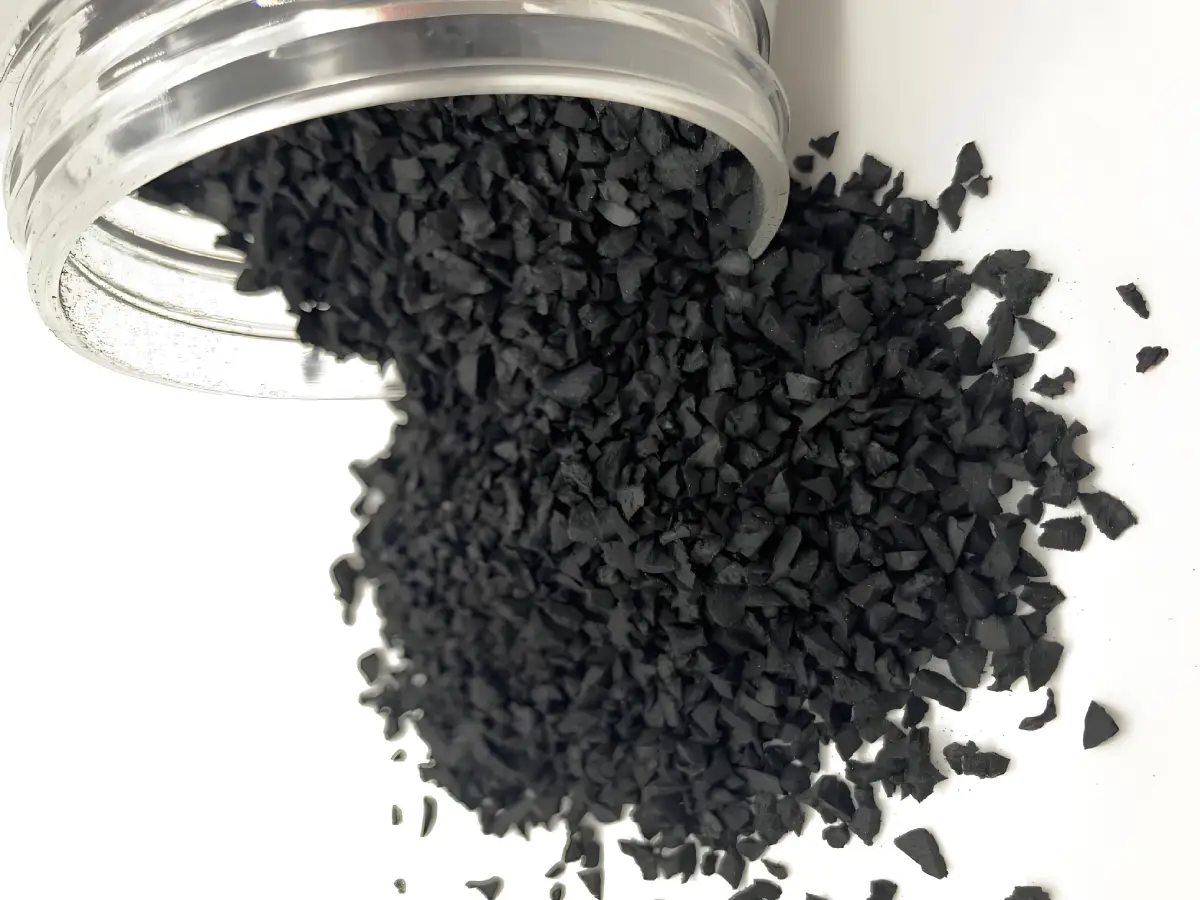
Replacement Materials for SBR Rubber Granules
EPDM Rubber Granules
Made from virgin rubber
Resists UV fading and heat buildup
Available in vibrant, non-staining colors
Thermoplastic Elastomers (TPE)
100% recyclable and odor-free
Maintains flexibility in extreme temperatures
Used in playgrounds and gym floors
Polyurethane-Bound Recycled Rubber
Combines recycled rubber with low-VOC binders
Reduces landfill waste by 75% vs. SBR
Terms | EPDM | SBR (From Old Tires) |
Colors | Many bright colors | Only black or gray |
Heat in Sun | Stays 35°F cooler | Gets very hot |
Smell | No smell | Strong rubber smell |
How Long It Lasts | 8-15 years | 2-5 years |
Comments
Products
Cases
Hot Sale Products
Lasted Blog
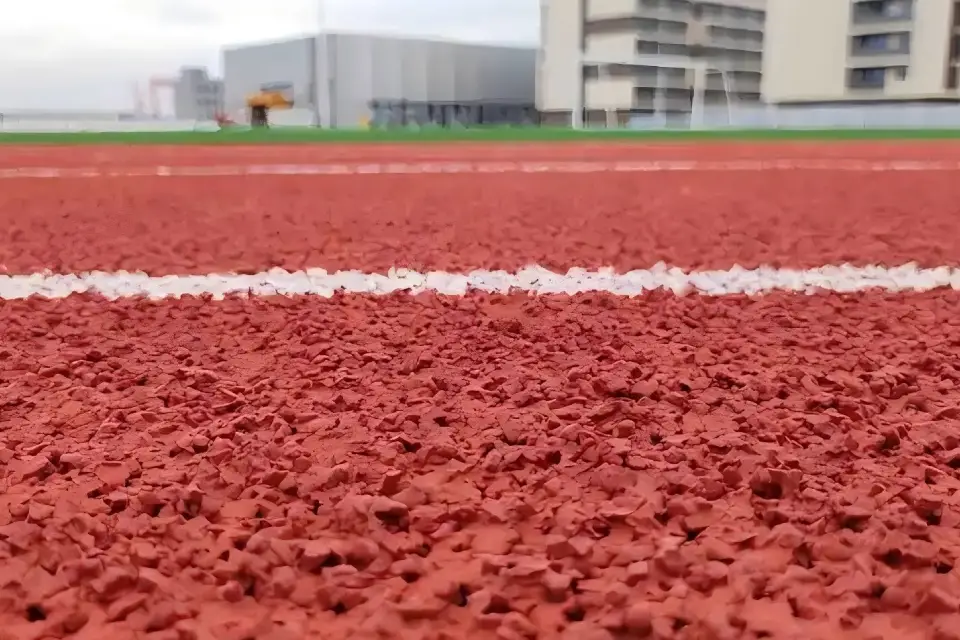
What is a Polyurethane Running Track?
When you watch the Olympics or the World Athletics Championships, behind those iconic burgundy tracks lies a material technology that has changed modern sports – polyurethane track (PU Track).
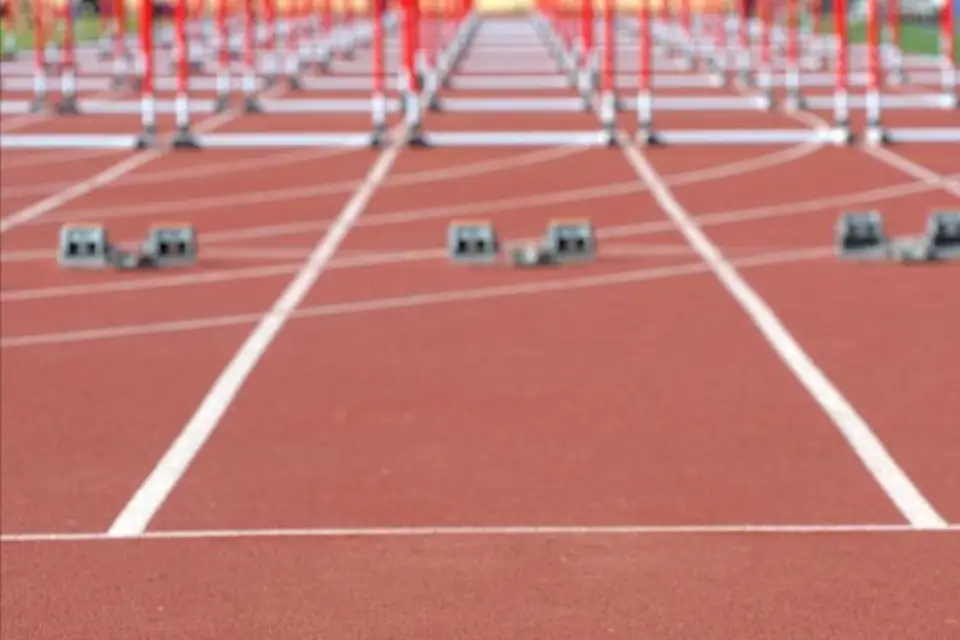
How to Maintain Athletic Running Tracks
Athletic tracks are durable. With regular maintenance, their service life can be significantly extended.
The following points should be noted during daily use and maintenance.
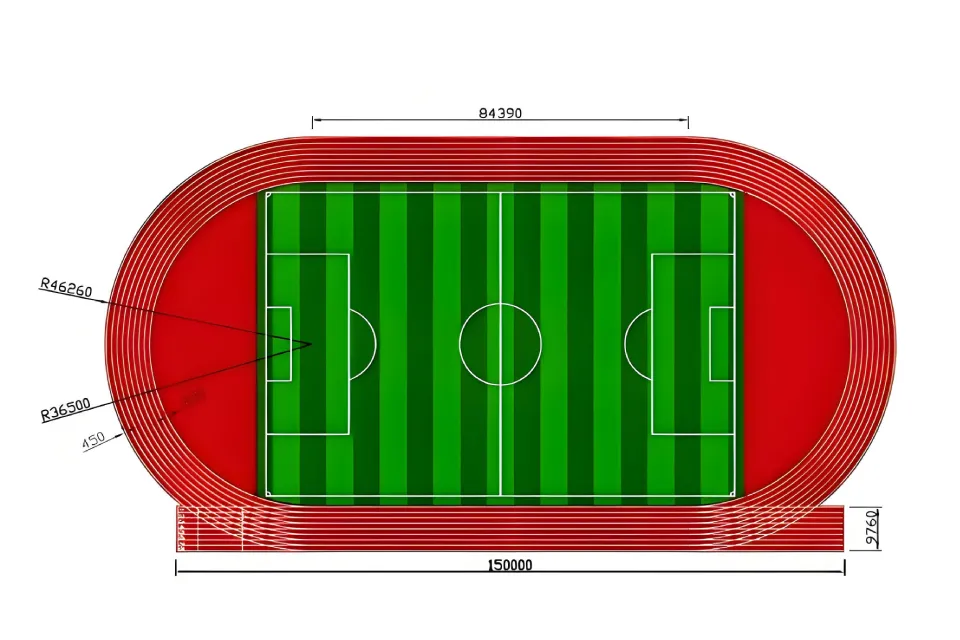
International Standards for Athletic Track Construction
As the core facility of competitive sports, the construction standards of athletic track are directly related to the performance of athletes’ competitive level and the fairness of competition.
Contact Us
- [email protected]
- +86-25 58933771
- Qiaolin Industrial Park, Pukou district, Nanjing city
Tags
Related Blogs
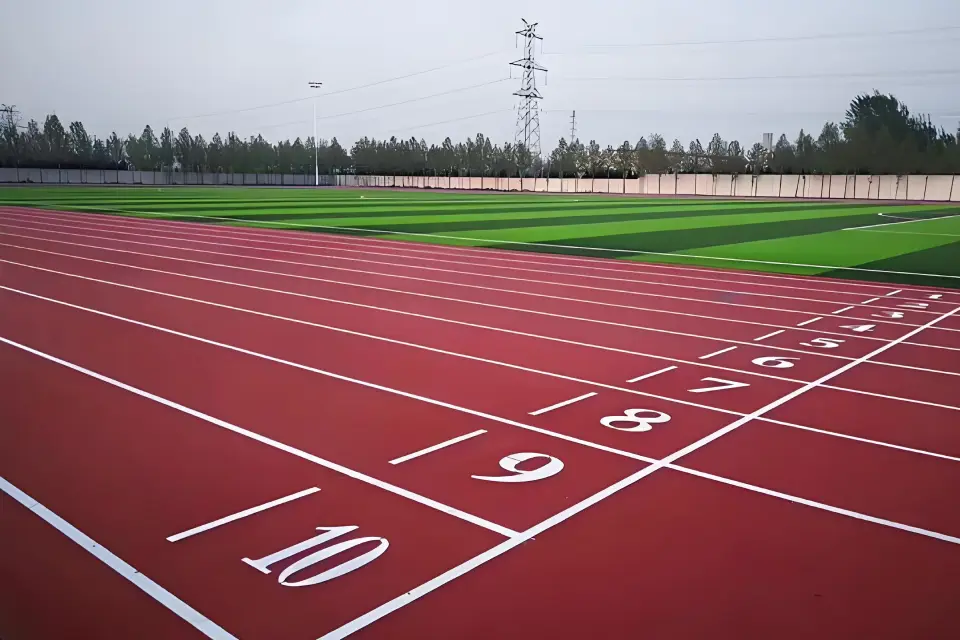
What are Athletics Tracks Made of
This blog post explores the fascinating world of running track surfaces, from traditional cinder tracks to state-of-the-art polyurethane and synthetic marvels.
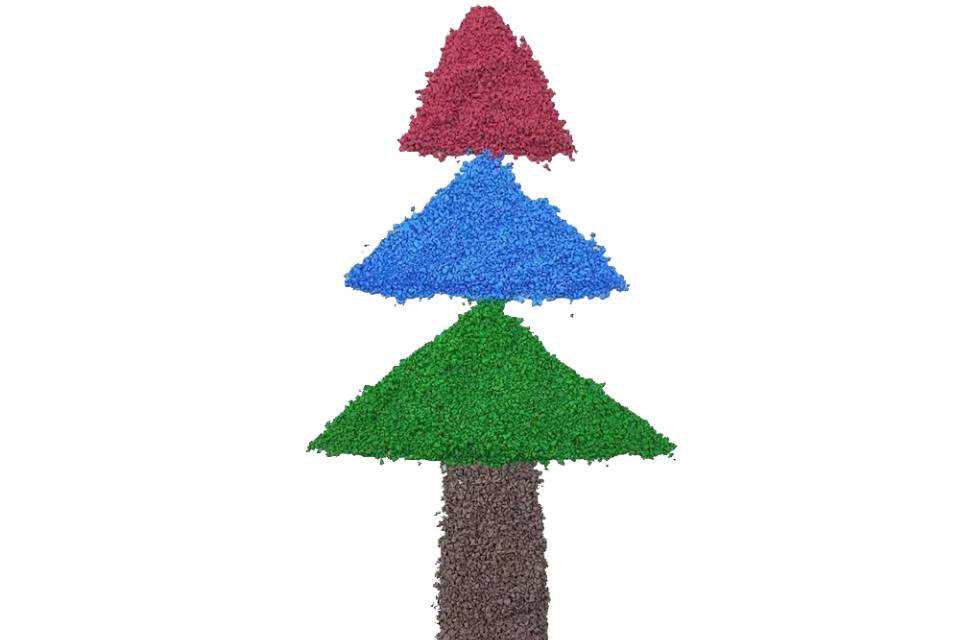
What is the Size of Epdm Granules
This article dives deep into the fascinating world of EPDM granules, exploring their diverse colors, sizes, and applications, with a special focus on their crucial role in creating safe, durable, and visually appealing playground flooring.
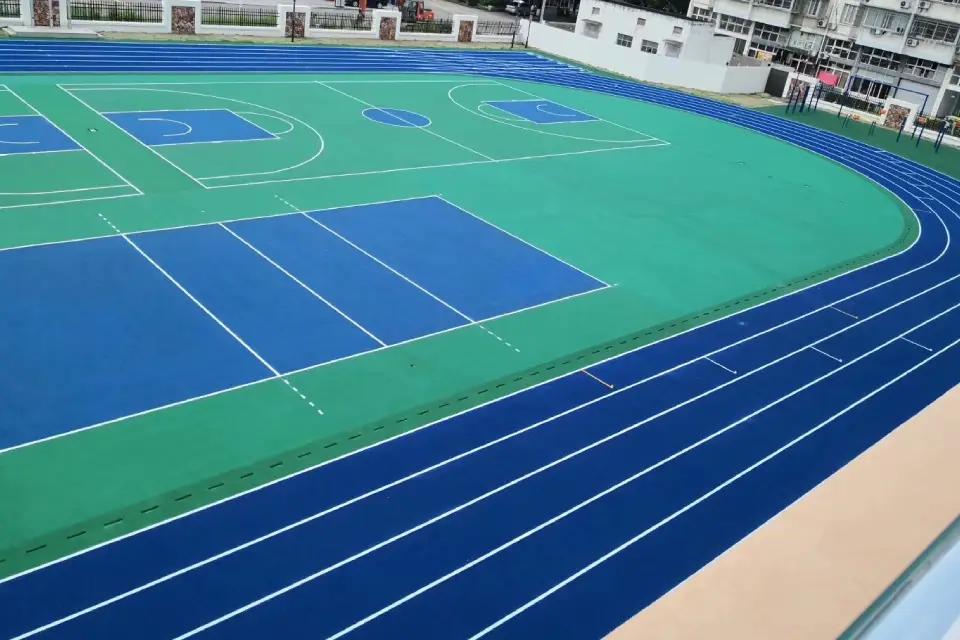
How to Build a Rubber Running Track
This article provides a comprehensive overview of running track construction, focusing on the intricacies of building a rubber running track suitable for various athletics events.