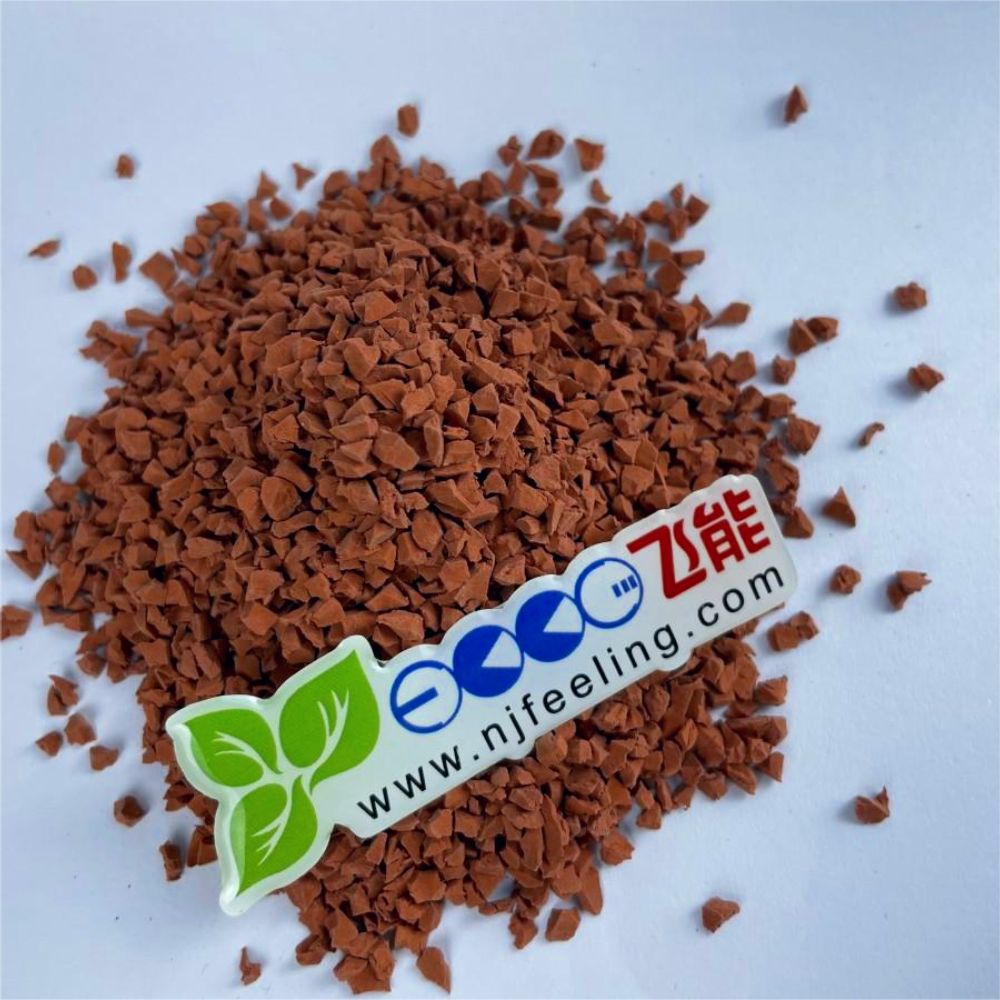
Step-by-Step Guide to Prefabricated Rubber Track Installation
Table of Contents
This article will analyze in detail the material characteristics, construction process and core advantages of prefabricated rubber tracks to help you select materials scientifically and create a cost-effective sports space!
Core Advantages of Prefabricated Rubber Tracks
- Efficient construction, shortening the construction period by 70%. Factory prefabricated forming coils, directly paved on site, no need for on-site mixing and paving, the construction cycle only takes 3-5 days (traditional processes require 20-30 days).
- Environmentally friendly and pollution-free, zero solvent volatilization, in line with GB 36246-2018 environmental protection standards (TVOC≤0.05mg/m³), can be put into use 24 hours after completion.
- Excellent performance, strong UV resistance and weather resistance (-30℃~80℃ without cracking), service life of more than 10 years;
- Stable friction coefficient (0.6-0.8), impact absorption rate ≥35%, protect the joints of athletes.
- Low maintenance cost, dense and smooth surface, stains can be wiped clean, no need to regularly replenish particles or renovate coatings.
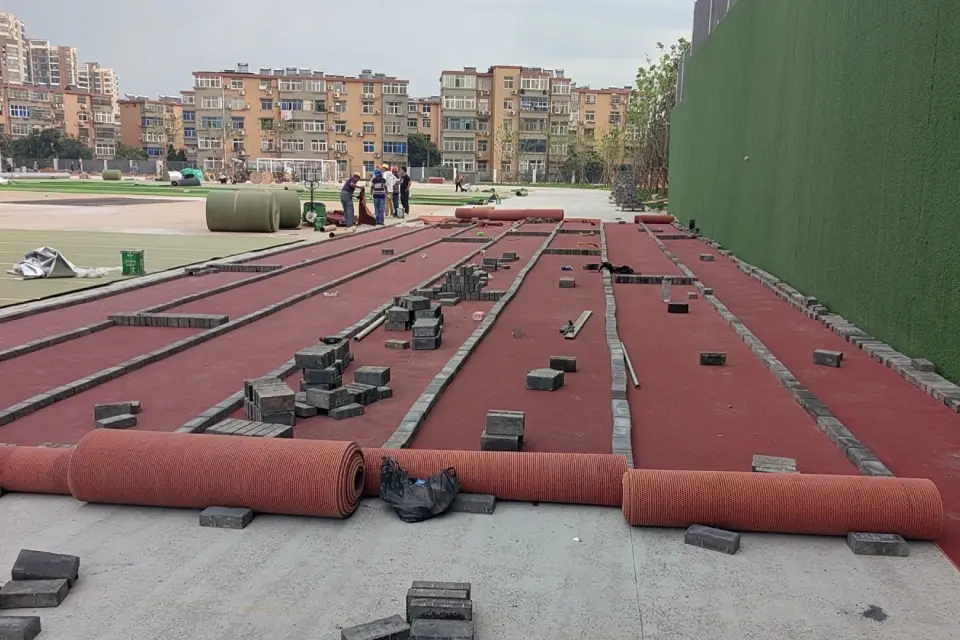
The Whole Process of Prefabricated Rubber Track Construction
Foundation treatment (key steps)
Surface requirements:
- Cement foundation: strength ≥ C25, flatness ≤ 3mm/3m, moisture content ≤ 5%;
- Asphalt foundation: porosity 3%-5%, no oil stains, no cracks.
Treatment process:
- Grind and clean the surface, inject epoxy resin glue into the cracks;
- Roller coating interface agent (enhance the adhesion of the roll material).
Roll material paving (standardized operation)
- Positioning and laying out: The laser laying out instrument calibrates the track boundary, with an error of ≤ 1cm;
- Laying the roll material:
- Unfold the roll material according to the design drawing and relax it naturally for 24 hours;
- Apply special glue (amount 1.5kg/㎡), compact and exhaust;
- The hot air gun in the curve area assists in shaping to ensure accurate curvature.
Joint and edge treatment
- Joint process: hot melt welding (temperature 130-140℃), tensile strength ≥50N/cm;
- Edge closing: polyurethane sealant filling to prevent warping and water seepage.
Line marking and maintenance
- Line marking construction: hot melt paint marking, line width 5cm±1mm, in line with IAAF standards;
- Finished product maintenance: closed for 48 hours, temperature >10℃, no trampling.
Precautions for Prefabricated Track Construction
Environmental requirements
- Construction temperature 10℃~40℃, air humidity ≤75%;
- Operation is prohibited on rainy and windy days.
Material acceptance
- Check the thickness of the coil (13mm±0.5mm) and surface flatness;
- Request an environmental protection test report (heavy metal, TVOC data).
Equipment selection
- Use professional hot melt welding machine and laser leveler to ensure process accuracy.
Precautions for Prefabricated Track Construction
Qualification Verification
- IAAF (WA) or China Athletics Association certification;
- ISO 9001 quality management system, environmental protection ten-ring certification.
Case Study
- IAAF (WA) or China Athletics Association certification;
- ISO 9001 quality management system, environmental protection ten-ring certification.
Service guarantee
- Quality warranty ≥ 8 years, free regular inspection service.
Comments
Products
Cases
Hot Sale Products
Lasted Blog
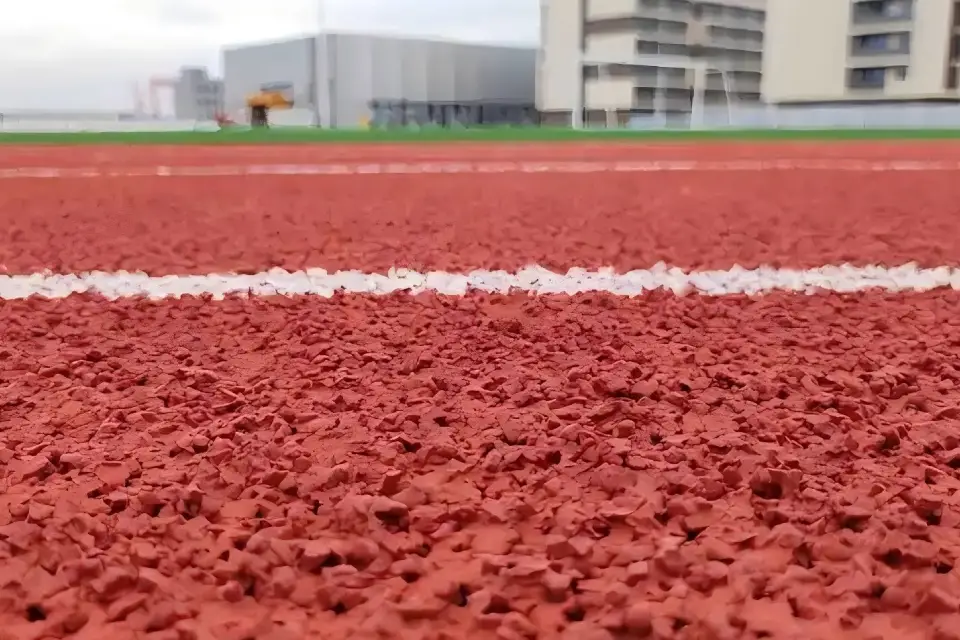
What is a Polyurethane Running Track?
When you watch the Olympics or the World Athletics Championships, behind those iconic burgundy tracks lies a material technology that has changed modern sports – polyurethane track (PU Track).
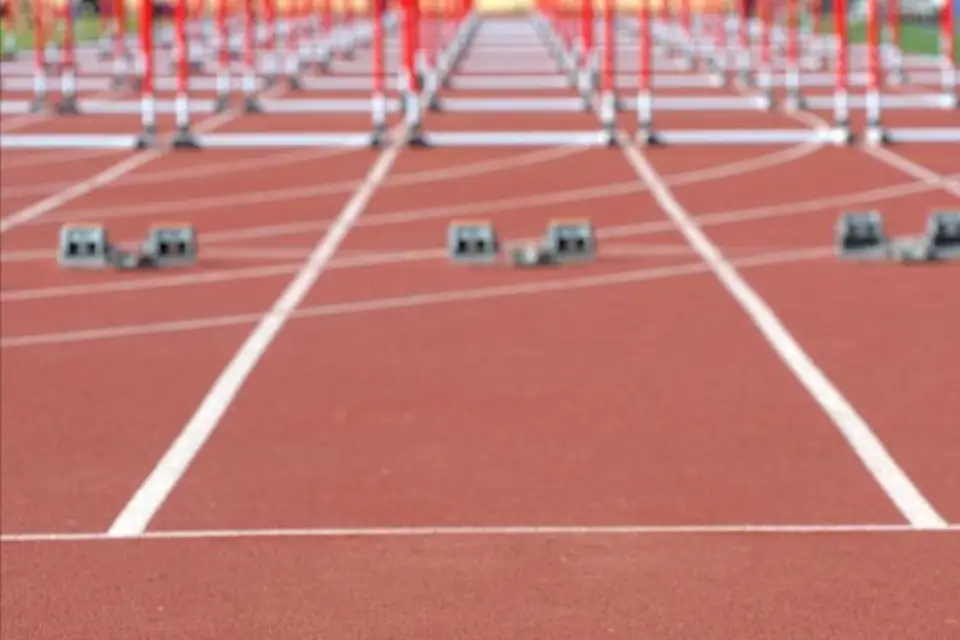
How to Maintain Athletic Running Tracks
Athletic tracks are durable. With regular maintenance, their service life can be significantly extended.
The following points should be noted during daily use and maintenance.
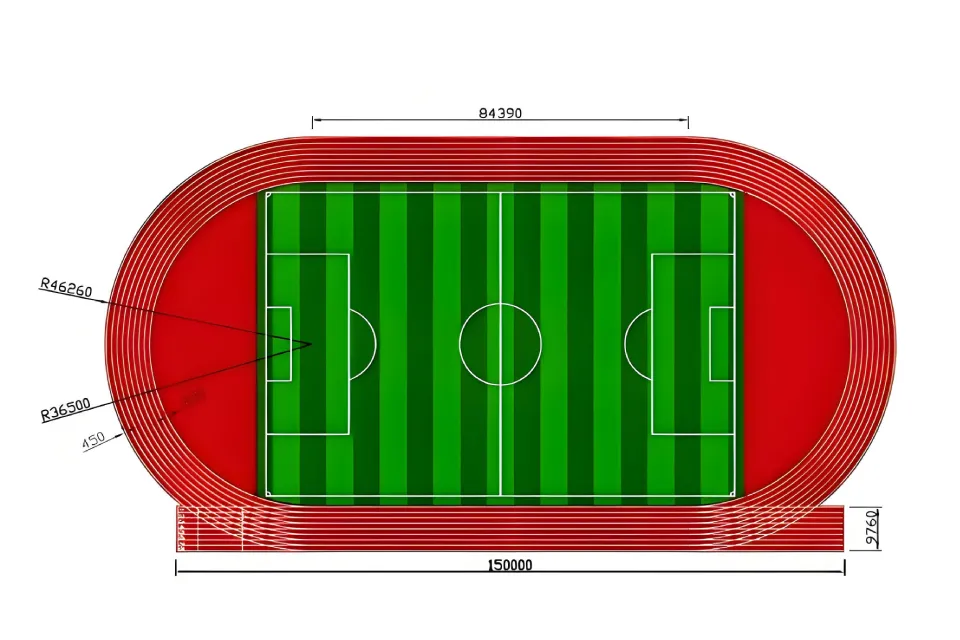
International Standards for Athletic Track Construction
As the core facility of competitive sports, the construction standards of athletic track are directly related to the performance of athletes’ competitive level and the fairness of competition.
Contact Us
- [email protected]
- +86-25 58933771
- Qiaolin Industrial Park, Pukou district, Nanjing city
Tags
Related Blogs
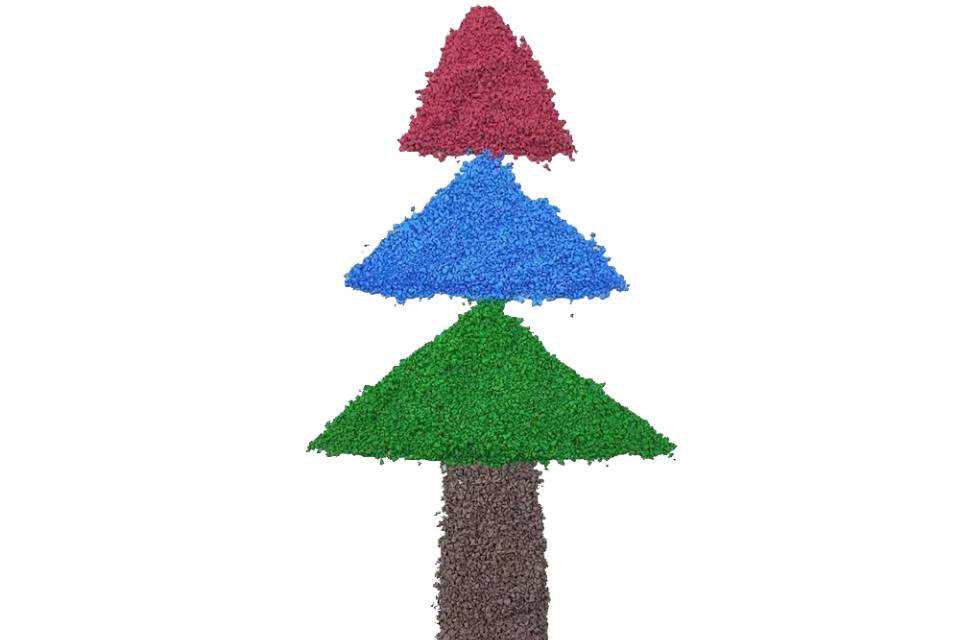
What is the Size of Epdm Granules
This article dives deep into the fascinating world of EPDM granules, exploring their diverse colors, sizes, and applications, with a special focus on their crucial role in creating safe, durable, and visually appealing playground flooring.
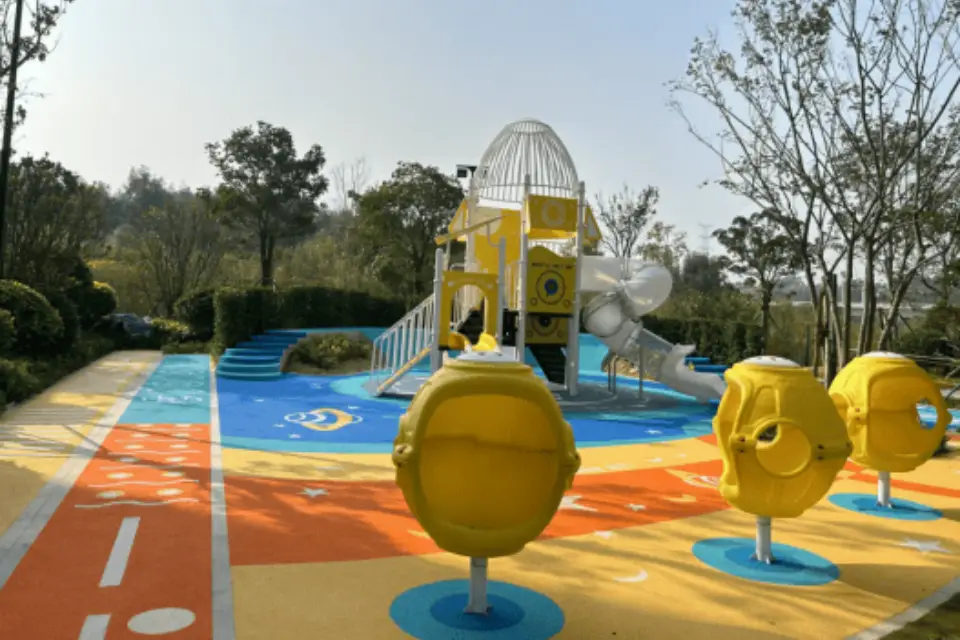
EPDM Rubber Flooring: Ground Guards to Protect Sports Safety
On the colorful ground of children’s playgrounds and campus tracks, EPDM granules are reshaping our public space with an annual market growth rate of 18%.
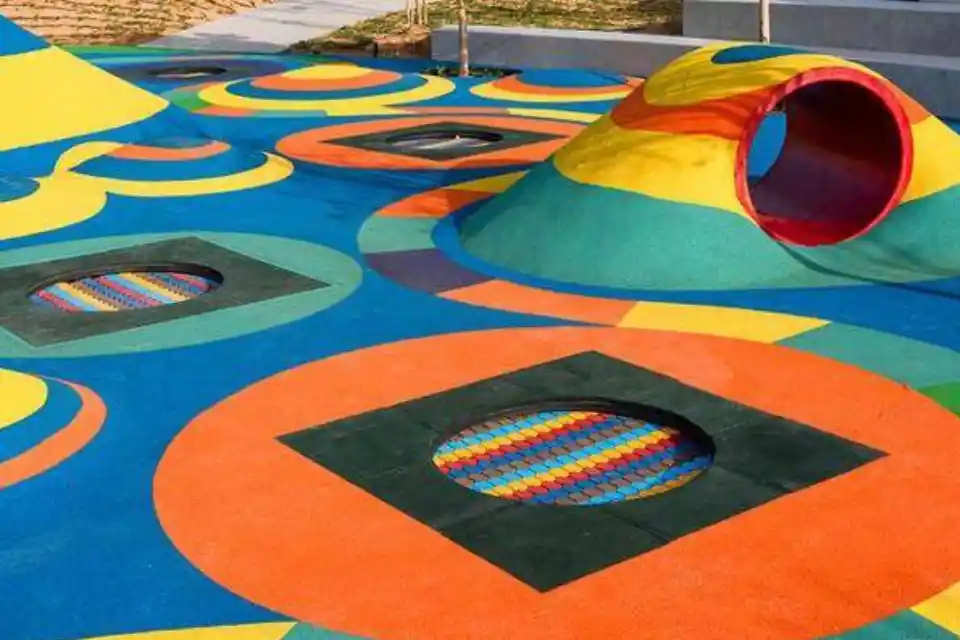
EPDM Granule Track Color Matching Guide
In recent years, EPDM plastic tracks have become the “new favorite” of schools, communities, parks and other places due to their environmental protection, durability and rich colors.