
Typer løpebaneoverflater for friidrett
Innholdsfortegnelse
Velge en løpebaneoverflate: Din guide til de forskjellige typene løpebaneoverflater
Fra polyuretan og gummi løpebanealternativer til syntetiske banealternativer, fordyper vi oss i egenskapene, fordelene og ulempene ved hver type løpebane. Enten du er leder for idrettsanlegg, trener eller idrettsutøver, er det viktig å forstå nyansene til løpebaneoverflater for å velge en løpebane som oppfyller dine spesifikke behov. Denne guiden hjelper deg med å velge riktig underlag for friidrettsbanen din, noe som gjør den til en må-lese for alle som er involvert i sportskonstruksjon eller friidrettsanlegg.
Hva er hovedtypene for løpebaneoverflater?
Grovt sett kan løpebaneoverflater kategoriseres i to hovedtyper: naturlig og syntetisk. Naturlige spor, som jordspor og slaggspor, var historisk vanlige, men er nå i stor grad erstattet av moderne løpebaner med syntetiske overflater i de fleste konkurrerende miljøer. Syntetiske spor gir flere fordeler i forhold til naturlige overflater, inkludert bedre støtdemping, mer konsistente ytelsesegenskaper og brukervennlighet i all slags vær. De er også kjent for å være ekstremt holdbare.
Innenfor kategorien syntetiske underlag er det flere typer løpebaneunderlag å vurdere. Gummi-løpebaneoverflater, inkludert de som er laget med lateks- eller polyuretanbindemidler og EPDM- eller gummigranulat, er populære på grunn av deres spenst og dempende egenskaper. Spesielt polyuretanbaneoverflater regnes ofte som gullstandarden for atletiske konkurranser på høyt nivå på grunn av deres holdbarhet, reaksjonsevne og evne til å tilpasses spesifikke ytelseskrav. Spor er ofte laget av disse materialene. Det riktige materialet som brukes for hvert prosjekt vil avhenge av flere faktorer.
Dirt and Cinder Tracks: Et tilbakeblikk på tradisjonelle løpeoverflater
Før fremkomsten av syntetiske overflater, var jordspor og slaggbaner normen for friidrett. Jordspor, laget av komprimert jord, var det enkleste og rimeligste alternativet. Imidlertid var de svært utsatt for værforhold, og ble gjørmete og ujevne når de var våte og støvete når de var tørre. Denne inkonsekvensen gjorde dem mindre enn ideelle for konkurrerende løping, siden overflaten kan påvirke en løpers ytelse betydelig. Den ujevne overflaten kan også føre til alvorlige skader.
Cinder tracks, som brukte et lag med cinders (et biprodukt av kullforbrenning) over en komprimert base, ga en liten forbedring i forhold til skittspor. De ga bedre drenering og en mer jevn overflate, men de var fortsatt langt fra perfekte. Cinder-spor kan være slitende, forårsake riper og fall, og de krevde regelmessig vedlikehold for å holde dem i vater og fri for rusk. Mens grusveier og slagtebaner sjelden brukes i moderne friidrett, representerer de en viktig del av friidrettshistorien. Du bør unngå denne typen banedekker.
Asfaltbaner: et rimelig alternativ for rekreasjonsbruk
Asfaltspor representerer et steg opp fra jordspor og slaggspor når det gjelder holdbarhet og konsistens. Disse sporene er laget av en blanding av tilslag og bitumen, det samme materialet som brukes i veibygging. Asfaltbaner gir et hardt, glatt underlag som er mindre påvirket av værforhold enn naturlige underlag. De er også relativt rimelige å bygge, noe som gjør dem til et populært valg for rekreasjonsfasiliteter, skoler og samfunnsspor. Installasjonen er også veldig enkel.
Asfaltbaner har imidlertid noen ulemper, spesielt for konkurrerende friidrett. Den harde overflaten gir lite støtdemping, noe som kan øke risikoen for skader for løpere, spesielt over lange distanser. Asfaltbaner kan også bli veldig varme i direkte sollys, noe som gjør dem ukomfortable å bruke i sommermånedene. Mens asfaltbaner kan være et passende alternativ for rekreasjonsløping og trening, anbefales de generelt ikke for konkurranser på høyt nivå. Disse banene laget av asfalt brukes nå sjelden til konkurranser.
Rubber Running Tracks: The Rise of Resilient Surfaces
Gummi løpebaneoverflater markerte et betydelig fremskritt innen løpebaneteknologi. Disse sporene består vanligvis av en gummioverflate laget av syntetiske materialer, som lateks eller polyuretan, kombinert med gummigranulat. Gummiløpebaner gir flere fordeler fremfor asfaltbaner og naturlige underlag. De gir en mer spenstig og støtdempende overflate, som reduserer belastningen på løpernes ledd og bidrar til å forhindre skader. De anses å være allværsoverflater og er ugjennomtrengelige for vær.
Gummiløpebaner er også kjent for sin holdbarhet og lave vedlikeholdskrav. De tåler hard bruk og ulike værforhold uten vesentlig forringelse. Gummioverflater kan enten være porøse eller ugjennomtrengelige, avhengig av den spesifikke konstruksjonen og materialene som brukes. Porøse overflater lar vann renne gjennom, mens ugjennomtrengelige overflater ikke gjør det. Valget mellom en porøs eller ugjennomtrengelig gummibane avhenger av faktorer som klima, budsjett og tiltenkt bruk. Det er også viktig å velge et godt installasjonsfirma.
Polyuretanbaner: Gullstandarden for konkurransedyktig friidrett?
Polyuretanbaner er ansett som gullstandarden for konkurrerende friidrett, spesielt på de høyeste nivåene av sporten. Disse syntetiske overflatene er laget av en kombinasjon av polyuretanharpiks og gummigranulat, og skaper en sømløs, spenstig og høyytelses løpeoverflate. Polyuretanbaneoverflater er kjent for sin eksepsjonelle holdbarhet, konsistente ytelsesegenskaper og evnen til å være innstilt for å møte spesifikke atletiske krav. De er enkle å vedlikeholde og krever lite vedlikehold.
World Athletics, det internasjonale styringsorganet for friidrett, har spesifikke standarder for polyuretanbaner som brukes i sanksjonerte konkurranser. Disse standardene dekker faktorer som overflatetykkelse, støtdemping, energigjenoppretting og sklisikkerhet. Evnen til polyuretanbaner til å møte disse strenge kravene gjør dem til det foretrukne valget for store internasjonale begivenheter, som OL og verdensmesterskap. Polyuretanoverflater er også svært værbestandige. Mens polyuretanbaner kan være dyrere å installere enn andre typer løpebaneoverflater, gjør deres ytelse, levetid og lave vedlikeholdskrav dem til en verdifull investering for seriøse friidrettsprogrammer.
Forstå forskjellen mellom porøse og ugjennomtrengelige syntetiske overflater
Når det gjelder syntetiske baneoverflater, er en viktig forskjell om de er porøse eller ugjennomtrengelige. Porøse overflater, også kjent som permeable overflater, er designet for å la vann renne gjennom overflaten og inn i de underliggende lagene. Dette oppnås typisk ved å bruke en relativt åpen struktur i overflatelaget, med større granulatstørrelser og et bindemiddel som ikke fyller hulrommene mellom granulatene helt. Porøse syntetiske overflater gir flere fordeler, inkludert utmerket drenering, redusert risiko for vannplaning og en litt mykere følelse under føttene. De er ekstremt slitesterke og spenstige.
Ugjennomtrengelige overflater er derimot utformet for å hindre vann i å trenge inn i overflaten. Disse overflatene har typisk en tettere struktur, med mindre granulatstørrelser og et høyere bindemiddelinnhold som skaper et solid, ikke-porøst topplag. Ugjennomtrengelige syntetiske overflater er ofte foretrukket i situasjoner der det er viktig å hindre vann i å nå de underliggende lagene, for eksempel når banen er laget på en betong- eller asfaltunderlag som kan bli skadet av fukt. Ugjennomtrengelige overflater kan også være foretrukket i visse klimaer eller for spesifikke atletiske begivenheter der en fastere, mer konsistent overflate er ønsket. Valget mellom porøse og ugjennomtrengelige overflater avhenger av faktorer som klima, budsjett, tiltenkt bruk og de spesifikke kravene til idrettsanlegget. Begge typer overflater krever også forskjellig vedlikehold.
Hva er nøkkelfaktorene å vurdere når du velger en løpebaneoverflate?
Å velge riktig løpebanedekke innebærer nøye vurdering av flere nøkkelfaktorer.
- Tiltenkt bruk: Vil banen primært brukes til trening, rekreasjonsløping eller konkurranser på høyt nivå? Ulike typer løpebaneunderlag er bedre egnet til ulike bruksnivåer.
- Klima: Lokale værforhold, som temperaturvariasjoner, nedbør og UV-eksponering, kan påvirke ytelsen og levetiden til en løpebaneoverflate betydelig.
- Budsjett: Startkostnaden for installasjon og de langsiktige vedlikeholdskostnadene varierer betydelig mellom ulike typer spor.
- Vedlikeholdskrav: Noen overflater krever mer vedlikehold enn andre. Vurder ressursene som er tilgjengelige for løpende vedlikehold.
- Ytelsesegenskaper: Faktorer som støtdemping, energiretur og sklimotstand kan påvirke utøverens ytelse og sikkerhet.
- Holdbarhet: Hvor godt vil overflaten tåle hard bruk, værforhold og andre potensielle kilder til slitasje?
- Estetikk: Utseendet til banedekket kan være viktig, spesielt i høyprofilerte omgivelser.
- Tilgjengelighet: Er underlaget egnet for idrettsutøvere med nedsatt funksjonsevne?
Ved å veie disse faktorene nøye, kan du ta en informert avgjørelse og velge en løpebanedekke som best dekker behovene til ditt idrettsanlegg. Slik velger du riktig type spor.
Installasjonsprosess: Hvordan installeres en syntetisk løpebane?
Installasjonen av en syntetisk løpebane er en flertrinnsprosess som krever spesialisert utstyr og ekspertise. Det første trinnet er vanligvis forberedelse av stedet, som kan innebære å grave ut den eksisterende overflaten, sortere området og installere en passende base. For polyuretan og andre høyytelsesbaner er underlaget ofte laget av asfalt eller betong, som gir et stabilt og solid fundament. Betong- eller asfaltbunnen må installeres riktig.
Når basen er på plass, påføres de syntetiske overflatelagene. For en støpt polyuretanbane involverer dette vanligvis å blande polyuretanharpiks med gummigranulat på stedet og deretter helle blandingen på basen. Overflaten blir deretter forsiktig sparklet og jevnet for å skape et sømløst og jevnt lag. Flere lag kan påføres, hvor topplaget ofte består av farget EPDM-granulat for økt UV-motstand og estetikk. Etter at overflaten er installert, må den herde i en periode, vanligvis flere dager, før den kan brukes. Løpebaneinstallasjonsprosessen må utføres av fagfolk.
Skritt | Beskrivelse | Betraktninger |
---|---|---|
1. Områdevurdering og planlegging | Evaluer de eksisterende forholdene på stedet, inkludert jordtype, drenering og topografi. Bestem passende spordimensjoner, layout og overflatetype basert på tiltenkt bruk, budsjett og klima. | Eksisterende verktøy, tilgjengelighet, miljøfaktorer, lokale forskrifter |
2. Utgraving og gradering | Fjern eksisterende vegetasjon, jord eller gammelt overflatemateriale. Grader området for å oppnå riktig helling og drenering. Komprimer underlaget for å gi et stabilt fundament. | Gravedybde, jordpakking, dreneringshelling, erosjonskontroll |
3. Grunnkonstruksjon | Installer et underlag, vanligvis bestående av komprimert tilslag (pukk) eller asfalt. Grunnlaget gir stabilitet, drenering og en jevn overflate for de syntetiske lagene. | Grunntykkelse, materialtype, komprimeringstetthet, dreneringssystem |
4. Syntetisk overflateinstallasjon | ||
a) Primerpåføring (hvis nødvendig) | Påfør et primerstrøk på grunnlaget for å fremme vedheft av den syntetiske overflaten. | Primertype, påføringsmengde, tørketid |
b) Baselag (for systemer som er støpt på plass) | Bland resirkulerte gummigranulat (f.eks. SBR) med et polyuretanbindemiddel. Hell og sparkle blandingen på basislaget for å lage et spenstig, støtdempende lag. | Grunnlagets tykkelse, gummigranulatstørrelse, bindemiddeltype, blandingsforhold, herdetid |
c) Slitasjelag (for systemer som er støpt på plass) | Bland EPDM gummigranulat med et polyuretanbindemiddel (ofte alifatisk for UV-stabilitet). Hell og sparkel blandingen på grunnlaget for å lage et slitesterkt, fargerikt og sklisikkert topplag. | Slitasjelagtykkelse, EPDM-granulatstørrelse og farge, bindemiddeltype, blandingsforhold, herdetid |
d) Prefabrikkert rulle- eller flisinstallasjon (for noen syntetiske systemer) | Legg ned prefabrikkerte ruller eller fliser av syntetisk gummimateriale over den forberedte basen. Fest rullene eller flisene til basen og til hverandre med passende lim. | Rulle/flisdimensjoner, materialtype, limtype, sømbehandling, kantbearbeiding |
5. Linjemerking og striping | Påfør spormerker og kjørefeltlinjer med spesialisert spormaling. Sørg for nøyaktige målinger og samsvar med relevante forskrifter (f.eks. World Athletics-standarder). | Malingstype, linjebredde, farge, refleksjonsevne, tørketid |
6. Herding og etterbehandling | La den syntetiske overflaten herde helt før bruk. Dette kan ta flere dager, avhengig av de spesifikke materialene og miljøforholdene. Gjennomfør en siste inspeksjon for å sikre riktig installasjon og kvalitet. | Herdetid, miljøforhold (temperatur, fuktighet), beskyttelse mot trafikk og rusk under herding |
7. Tilleggsinstallasjoner | Installer eventuelle tilleggsfunksjoner, som fortauskanter, dreneringskanaler, lengdehopp eller rullebaner for stavhopp, etter behov. | Integrasjon med baneoverflaten, materialkompatibilitet, sikkerhetshensyn |
Vedlikehold og vedlikehold: Sikre lang levetid for løpebanen din
Riktig vedlikehold er avgjørende for å sikre lang levetid, ytelse og sikkerhet på løpebanen. Regelmessig rengjøring er en av de viktigste aspektene ved vedlikehold. Banen bør holdes fri for rusk, som løv, skitt og kvister, som kan skade underlaget og skape snublefare. Du kan bruke en løvblåser, kost eller spesialisert banerengjøringsmaskin for å fjerne rusk. Syntetiske overflater krever generelt lite vedlikehold, men de må fortsatt rengjøres.
I tillegg til rengjøring er det viktig å inspisere baneoverflaten regelmessig for tegn på skade eller slitasje. Små sprekker eller hull kan ofte repareres ved hjelp av lappemidler eller spesialiserte sporreparasjonssett. Større skadeområder kan kreve oppmerksomhet fra en profesjonell løpebaneentreprenør. Avhengig av type overflate og bruksnivå, kan periodisk ny overflatebehandling eller overmaling også være nødvendig for å opprettholde banens ytelsesegenskaper og utseende. Med riktig pleie vil din syntetiske bane vare i mange år.
Fremtiden for løpebaneoverflater: Hva er det neste?
Feltet for løpebanebelegg er i stadig utvikling, med pågående forskning og utvikling rettet mot å forbedre ytelse, sikkerhet, bærekraft og kostnadseffektivitet. Et fokusområde er utvikling av nye materialer, som biobaserte polymerer og forbedrede gummiblandinger, som gir forbedrede ytelsesegenskaper samtidig som de reduserer miljøpåvirkningen. Noen produsenter utforsker også bruken av nanoteknologi for å lage overflater med forbedret holdbarhet, støtdemping og energiretur. Disse materialene kan skape en myk overflate som gjør at idrettsutøvere kan trene og konkurrere trygt.
En annen trend innen løpebanebelegg er den økende bruken av data og analyser for å optimalisere banedesign og konstruksjon. Ved å analysere idrettsutøvers biomekanikk og overflateinteraksjon, er forskere i stand til å finjustere egenskapene til baneoverflaten for å forbedre ytelsen og redusere risikoen for skade. Denne datadrevne tilnærmingen brukes også til å utvikle tilpassede overflater for spesifikke arrangementer eller individuelle idrettsutøvere. Ettersom teknologien fortsetter å utvikle seg, kan vi forvente å se enda flere innovative og høyytende løpebaneoverflater i årene som kommer. Løpeopplevelsen vil bare bli bedre og bedre med disse fremskrittene.
Konklusjon
Her er de 10 viktigste tingene å huske fra denne veiledningen:
- Løpebaneoverflater kan bredt kategoriseres i naturlige (smuss, slagg) og syntetiske (gummi, polyuretan, etc.) typer.
- Syntetiske overflater gir fordeler i forhold til naturlige overflater når det gjelder allværsbruk, støtdemping og ytelseskonsistens.
- Asfaltbaner er et rimelig alternativ for rekreasjonsbruk, men mangler demping og ytelsesegenskaper som kreves for konkurrerende friidrett.
- Gummi løpebaneoverflater gir spenst, støtdemping og holdbarhet, noe som gjør dem egnet for ulike nivåer av trening og konkurranse.
- Polyuretanbaner regnes som gullstandarden for idrettskonkurranser på høyt nivå, og oppfyller strenge ytelsesstandarder satt av organisasjoner som World Athletics.
- Syntetiske overflater kan enten være porøse (tillater vann å renne gjennom) eller ugjennomtrengelige (forhindrer vanninntrengning), avhengig av deres konstruksjon og tiltenkte bruk.
- Nøkkelfaktorer å vurdere når du velger en løpebaneoverflate inkluderer tiltenkt bruk, klima, budsjett, vedlikeholdskrav, ytelsesegenskaper, holdbarhet, estetikk og tilgjengelighet.
- Installasjonen av en syntetisk løpebane innebærer forberedelse av stedet, grunnkonstruksjon, påføring av syntetiske lag og herding.
- Riktig vedlikehold, inkludert regelmessig rengjøring, inspeksjoner og rettidige reparasjoner, er avgjørende for å sikre lang levetid og ytelse til en løpebaneoverflate.
- Fremtiden for løpebaneoverflater kan innebære nye materialer, datadrevet design og tilpasning for ytterligere å forbedre ytelse, sikkerhet og bærekraft.
Kommentarer
Produkter
Saker
Hot Salgsprodukter
Varte blogg
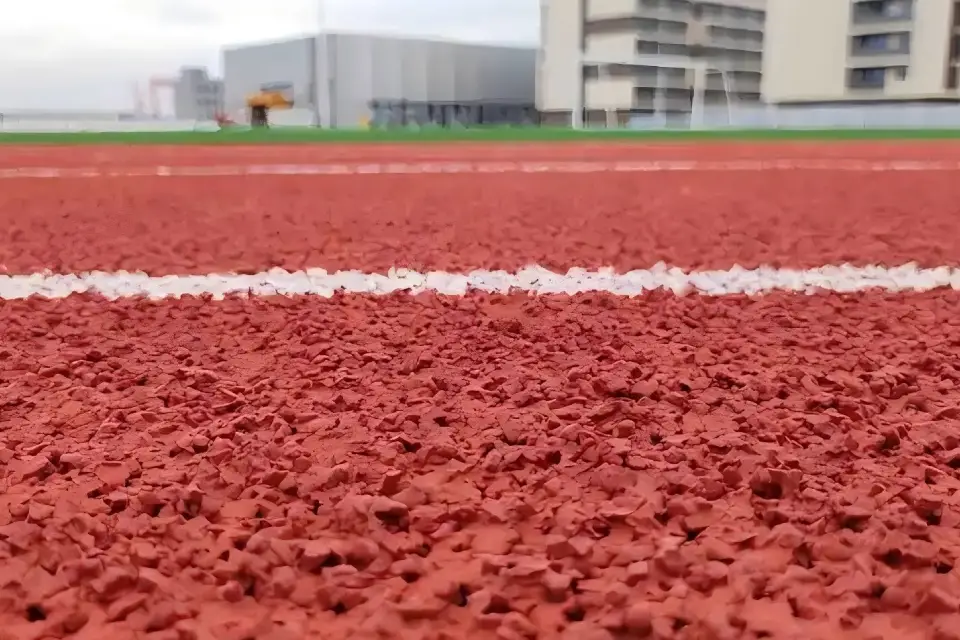
Hva er en løpebane i polyuretan?
Når du ser på OL eller friidretts-VM, ligger det bak de ikoniske burgunderfargede banene en materialteknologi som har forandret moderne idrett – polyuretanbaner (PU-baner).
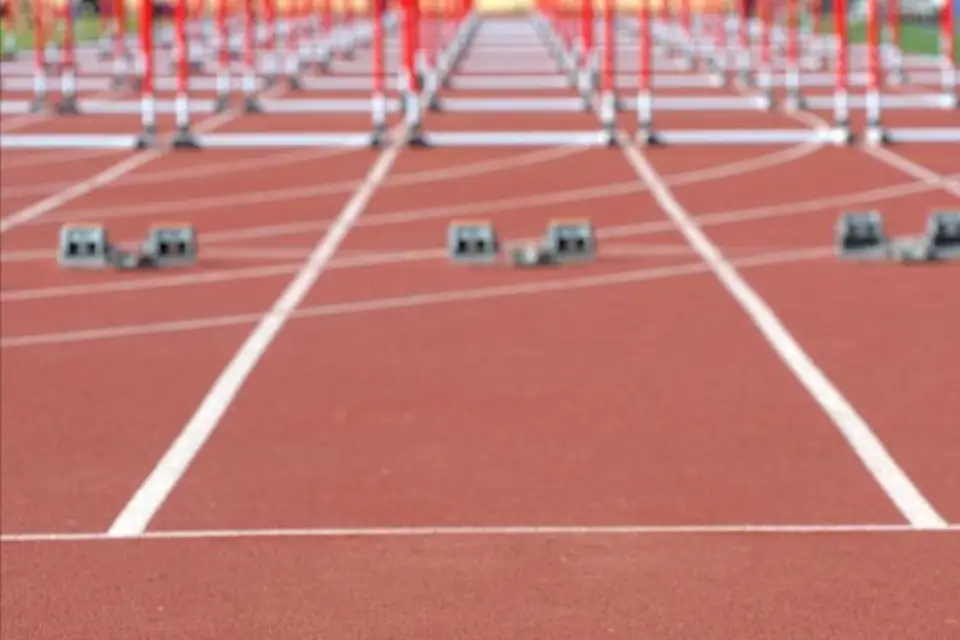
Slik vedlikeholder du løpebaner for atletiske løp
Idrettsbaner er slitesterke. Med regelmessig vedlikehold kan levetiden forlenges betraktelig.
Følgende punkter bør tas i betraktning ved daglig bruk og vedlikehold.
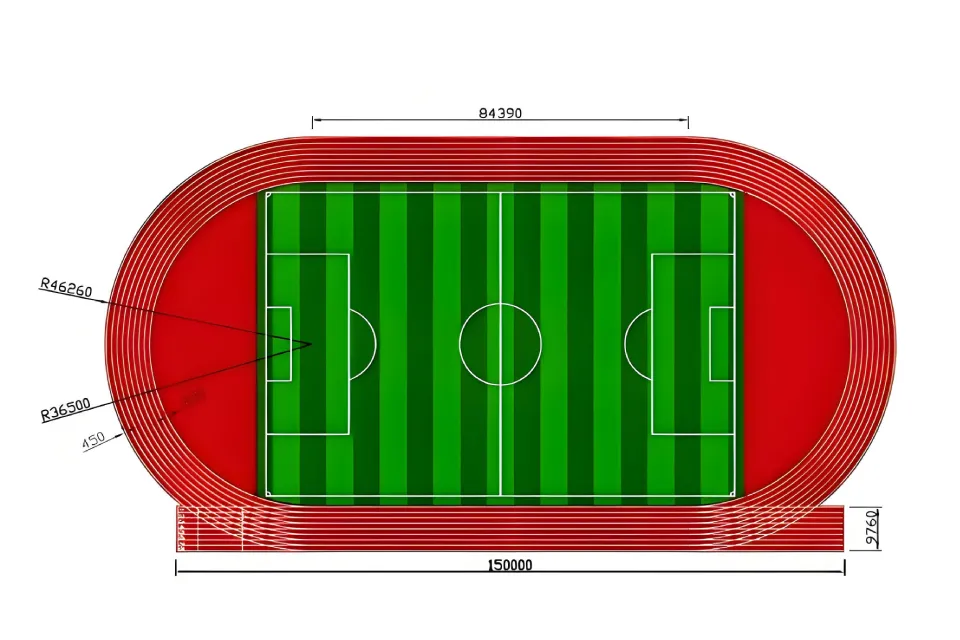
Internasjonale standarder for bygging av friidrettsbaner
Som kjerneanlegget for konkurranseidrett er konstruksjonsstandardene for friidrettsbaner direkte relatert til utøvernes konkurransenivå og rettferdigheten i konkurransen.
Kontakt oss
- [email protected]
- +86-25 58933771
- Qiaolin industripark, Pukou-distriktet, Nanjing by
Tagger
Relaterte blogger
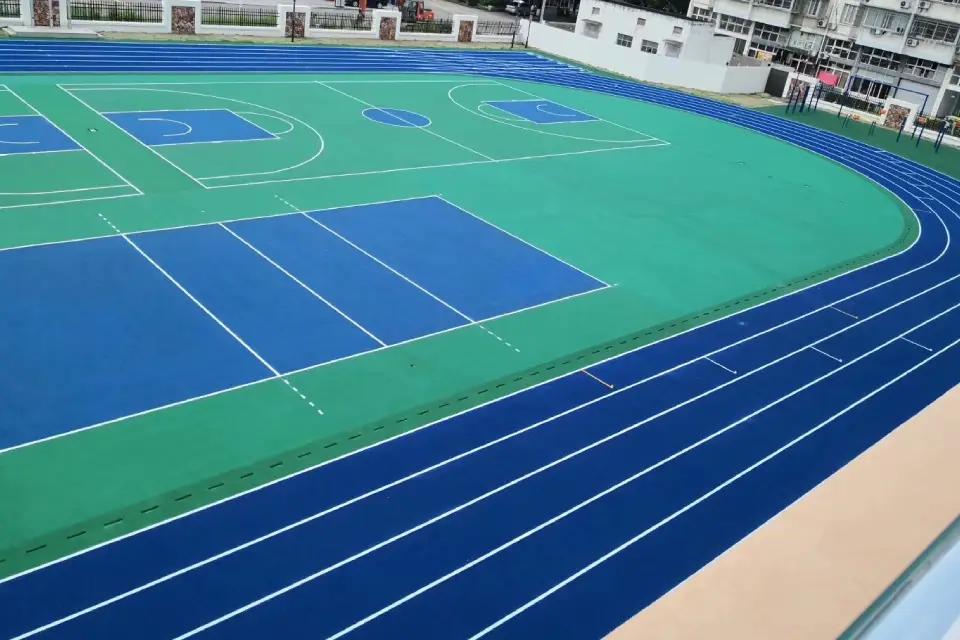
Hvordan bygge en løpebane i gummi
Denne artikkelen gir en omfattende oversikt over løpebanekonstruksjon, med fokus på vanskelighetene ved å bygge en løpebane i gummi som passer for ulike friidrettsarrangementer.
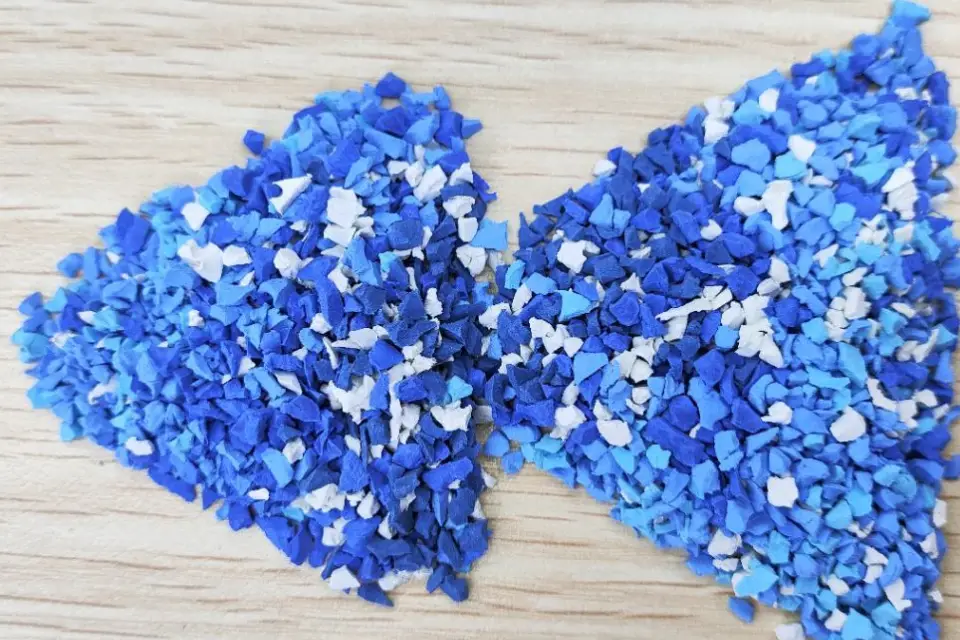
Bygging av rullestol EPDM gummiramper for funksjonshemmede
I en tid hvor samfunnet i økende grad er opptatt av reisevennligheten for funksjonshemmede, er bygging av ramper for rullestoler for funksjonshemmede av vital betydning.
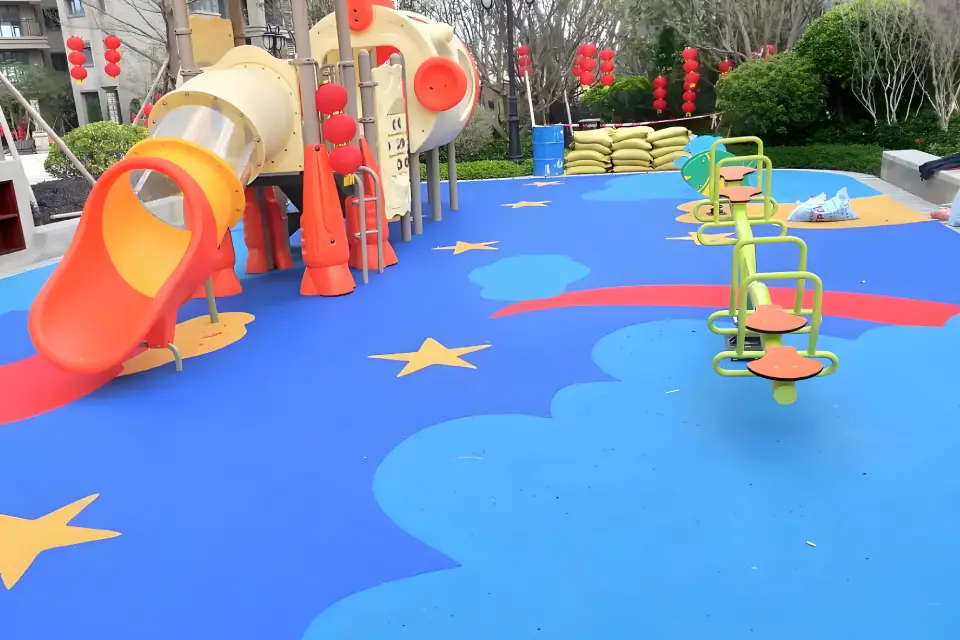
Ekspertguide til lekeplassoverflater i støpt gummi
Denne artikkelen dykker ned i verden av påstøpt gummibelegg, et populært valg for lekeplasser og andre rekreasjonsområder.